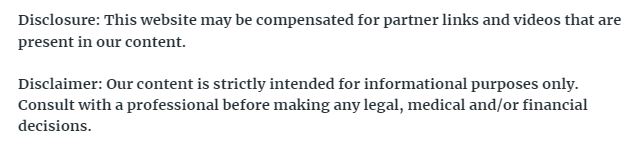
The molybdenum manufacturing process is a more important one than many people realize, are aware of, or give it the credit it deserves it for. After all, the molybdenum manufacturing process has been in use for decades, for centuries, dating back two hundred years. In fact, molybdenum was first discovered and then recognized as an element – and official element – right around the close of the eighteenth century, the end of the 1700s. Since then, the molybdenum manufacturing process and molybdenum manufacturing methods have been widely utilized and used across a large number and breadth of industries, as it is an element that has proven to have many uses.
One such thing that is important to know about molybdenum and the molybdenum manufacturing process, as will any manufacturing process, is the melting point of molybdenum. The overall melting point of molybdenum is a particularly high one, as the element will not melt until it reaches at least four thousand and seven hundred and forty eight degrees Fahrenheit. This means that the molybdenum manufacturing process must be adjusted accordingly in order to manufacture molybdenum in the most efficient of ways possible.
The molybdenum manufacturing process has also been widely utilized in part because of the character of the electrodes of molybdenum. As any molybdenum manufacturer is more likely than not to know, molybdenum is considered to be a substance and an element of high purity, with the ideal glass melting electrodes with a purity of at least ninety five percent, if not even higher – after all, when it comes to glass melting, the higher the purity the better. This purity is necessary, as high purity glass melting is less likely to be corrosive or susceptible to corrosion itself. This can also help to minimize any potential glass discoloration.
Tungsten is another important element that can be used for many of the same purposes as the molybdenum manufacturing process and tungsten products are wide spread – more wide spread than most are even aware of – in our country and in our world as a whole. As the element of tungsten has been found to be at least as twice as dense as steel, there are many important applications for the element in our world. It’s melting point is also impressive, at more than six thousand degrees Fahrenheit, and is even higher than the melting point of molybdenum, which in and of itself has an impressive and considerable melting point that should not be taken lightly. It also has the highest known tensile strength with a known tensile strength of one thousand and five hundred and ten megapascals.
At the end of the day, there are a number of elements such as tungsten and molybdenum that have many scientific as well as even many practical applications today in the modern world. However, it is important that we study these applications and use them responsibly, as well as determining which element is best for which use or application. The molybdenum manufacturing process is one such example of looking closely at the manufacturing process of an element and learning how to better it and to make it grow not only in its efficiency but in the science behind the element and the purposes for said element such as molybdenum. From the melting point of an element to the purity of its electrodes, there is more to the common and official element than often meets the eye of the general population – and there is still even so much more to learn.