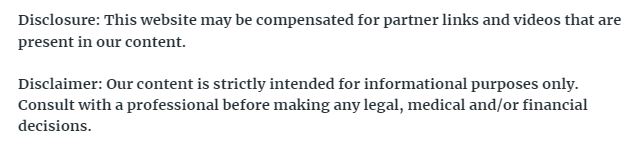

For many industrial settings, there is the need to maintain specific temperatures in certain areas. This is the case in many manufacturing industries as well as other areas, and at many industrial locations, requirements dictate the use of some form of cooling solution or the other. Whether it is in the petrochemical industry, pharmaceutical plants, power generation stations or just plain large scale HVAC systems for cooling medical facilities and public areas, there is always the need for high efficiency cooling in commercial settings, and most of these requirements are met through the use of commercial cooling towers. Water cooling towers and air cooling tower systems are used profusely in these industries, and these cooling solutions mainly come in two forms — open circuit or closed-circuit.
Both open and closed-circuit cooling towers ultimately serve the same purpose — to provide industrial cooling in an efficient manner, but they way they go about accomplishing this task is vastly different. In traditional open circuit cooling tower structures, large amount of fill or packing material is packed into an enclosed space, through which the water passes creating a large area of air-water interface. This helps the water to cool as it passes through the fill, until it is finally collected in a separate storage area for cold water at the bottom. The air, which in turn heats up and becomes more moist, is actually vented out into the atmosphere by appropriate venting mechanisms.
A closed-circuit cooling tower, however, works differently, incorporating a system that is essentially a closed loop. Also sometimes called a dry cooling tower, these systems work in a way such that the water actually never comes in contact with the air. Rather, it is distributed over two loops with one on the inside and one outside. The cascading flow of water through this outer circuit is what causes the air to be drawn in, providing evaporative cooling. These towers can also sometimes have separate heat exchange mechanisms, according to the amount of cooling and the volumes of water in the process required to achieve that cooling.
While both these systems can provide for optimum cooling in industrial circumstances, there are quite a few advantages of closed-circuit cooling towers that prompts many companies to opt for this mode of cooling. Essentially, the closed-circuit method of cooling, while being almost equally effective in terms of heat transfer as any wet cooling system, has the distinct advantage that the water does not come in contact with the air directly. It is a closed loop, and therefore, nothing is sent out to vent to the outside environment. This is useful on both counts, as it maintains the purity and integrity of the working fluid by preventing its contact from environmental factors and pollutants, thereby reducing the risk of contamination. The system also does not require any outside venting, which means that nothing harmful gets released into the atmosphere as well, terminating the need to conform to commercial emission specifications and guidelines.
The trick here is to know more in detail about these two different techniques of cooling and use that knowledge to figure out what mode of cooling would suffice for a particular set of industrial requirements. However, for the reasons mentioned above, many industries tend to opt for closed-circuit systems. For you to choose, it is best to consider these advantages and then to arrive at an informed decision. That way, you can ensure that your industrial settings receive the most apt and convenient cooling system, which would provide cost-effective cooling for you for many years.