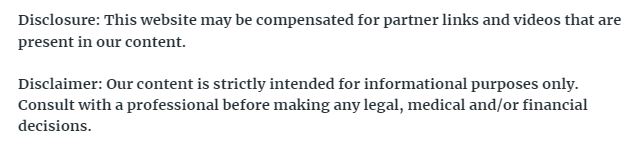

The packaging for pharmaceutical products is very important to the success of the product. Both the primary and secondary pharmaceutical packaging need to be matched perfectly to the product in question.
Blister packaging is a very popular form of secondary pharmaceutical packaging. It is used very often for unit or single dose pharmaceutical products in the United States. It often includes lamination that consumers can peel open and can be easier than other kinds of medical packaging techniques. Many blister packaging companies will include certain information about the product on the secondary pharmaceutical packaging such as the expiration date and lot number.
There are things pharmaceutical companies can do to make sure the packaging they use is right for their products.
1. Get the packaging company involved earlier in the process.
When you are working on developing a new pharmaceutical product, you may not be thinking about the proper primary and secondary pharmaceutical packaging but you should. All medical packaging companies are experts at packaging. They may be able to help you avoid some common problems that impact getting regulatory approval.
Another factor in this is the clinical trial process. You want to use the same packaging throughout the testing of your new pharmaceutical product. That eliminates any interaction between your primary and secondary pharmaceutical packaging and your product. For the purpose of proper testing, you need to limit the number of variable involved. That includes the packaging.
2. Identify problems early.
There are some problems that happen on a regular basis with certain kinds of pharmaceutical packaging. What sometimes can happen with blister packaging, is that there is not enough space around the cavity for the blister that can impact the ability to seal the package. Other problems that can be avoided are using the wrong temperature or pressure to seal the packaging.
The best way to avoid some of these problems is to get everyone together early in the process. Everyone needs to understand what will be needed for the proper manufacture of the packaging. So, you need your purchasing agents, packaging designers, representatives from your manufacturer and all of your vendors to understand the technical requirements of making the right packaging. Everyone needs to see the link between the packaging and the quality of the product itself.
3. Get you validation process down pat.
When this is approached in the right way, the validation process can increase your yield and decrease the amount of wasted materials. A properly conducted validation process will identify possible problems with the manufacturing process.
A properly executed validation process will make it easier to show compliance with all of the rules and regulations that are put on pharmaceutical products. The process provided the proper documentation of everything in the process and documents all of the quality control measures that are undertaken. This documentation will be helpful when dealing with the Food and Drug Administration (FDA).
4. Make sure you have customized the packaging for the product.
One of the great things about blister packaging designs is just how customized they can be. The main purpose of any packaging for any product from soda to pharmaceuticals is to protect it from degradation and contamination. In every industry, the right packaging can also be used in branding and marketing efforts for the product and the company that produces it.
In the case of most primary and secondary pharmaceutical packaging, care must be taken to customize the packaging for the specific product. The medication inside blister packaging needs to be protected from a number of threats such as oxygen, moisture, heat or cold. It also needs to be made to make one product have a much different look from other similar products that are on the market.
The packaging can also be designed to put a lot of information about the product on the package. For pharmaceutical products, this can include dosage information, possible side effects and the best way to take the medication.
The primary goal of the packaging is to get the product safely from the factory to the store shelves. If it fails in that area and people purchase foods or beverages that have gone bad, the company’s reputation can suffer. This is more serious for medications and the packaging process must reflect that.