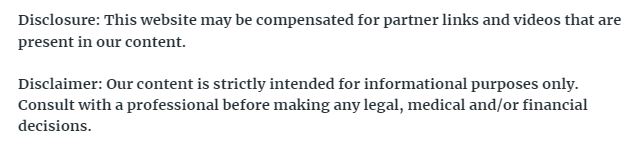
Taming the various forces of nature has always been a construction challenge for humanity for centuries. Anything from flooding waters to forest fires to earthquakes have factored into construction past and present, and even now, controlling water flow is a construction project necessary to maintain water levels along lakes, coast lines, or anywhere else where water is found. Retaining walls can act as miniature dams of sorts, keeping water on one side and preventing flow or leaks to the other. Controlling water flow can also help local areas manage irrigation, sewage, and other water based industries and work, and often, concrete is the material of choice for channel lining, civil construction, and other jobs. When controlling water flow is vital, concrete and a good contractor can get the job don.
The Power of Concrete
Concrete is a very common building material; so common, it is almost invisible in everyday life and taken for granted. There is a reason for this. Concrete stands as the most widely used human made material on earth, and with its ease of creation and application, not to mention strength, the appeal is clear. By volume, concrete is 60% to 75% aggregate, or gravel and sand, mixed with 15% to 20% water, 10% to 15% cement, and 5% to 10% air. What is more, concrete actually gets stronger over time rather than weaken, assuming extreme erosive forces are not at work, making it a great investment. There is a lot of production for this construction material; every year, more than two billion tons of cement alone is produced, and every year, six billion cubit meters of concrete is produced. Some contractor companies are based almost entirely on concrete, from preparing the area for pouring to setting up wood walls to pouring the concrete and smoothing it over. Few other materials can handle controlling water flow as concrete.
Controlling Water Flow
A civil construction company can get right to work controlling water flow with concrete projects. According to Allan Block, retaining walls keep the area behind them dry, and certain steps should be taken during construction. For one thing, the contractor should examine the site and determine from what direction the water will come, and how to manage it. While the wall is being built, materials should be staged so that surface runoff is directed properly, and infill soils and the project as a whole should be covered at the end of each work day to prevent rain water from ruining it.
In addition, walls four feet or taller should have a toe drain and wall rock that will remove incidental water from behind the wall without acting as the main drainage path. And during constriction, it may become necessary to grade the surrounding area so water does not flood into the construction site. Ground water, or water in soil, should not be allowed to touch the wall or the soil behind it during construction. Also, when a toe drain is installed in a wall four feet high or higher, the pipe should be vented every 50 feet at sites lower at the construction area. These drains should be clearly marked, such as with signs or yellow and black stripe patterns, so they are not accidentally damaged or blocked. Rodent screens can keep animals and debris out so water flow is not impeded.
Other areas with water may require concrete construction such as retaining walls or channels or drains. Irrigation canals build of concrete may need drain sites in the case of heavy rain, and industrial areas such as a factory of office building in a city may need such drainage in the case of heavy rain, or in low elevation areas, to protect the site from floods (man made or natural). Control of soil erosion is also possible by controlling water flow so land can stay arable. Rivers with unstable walls can be reinforced with concrete construction for stabilizing an embankment.