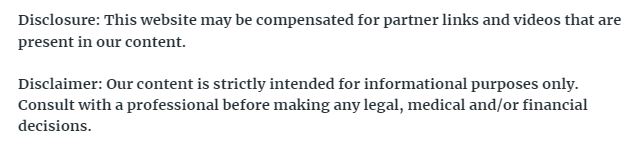

Knowing how to use the equipment on a worksite is one of the top ways to avoid accidents and improve worker safety. Since construction zones are always teeming with machinery and moving parts, it’s important that the people behind those moving parts, like lifting equipment, know exactly what they’re doing with the machines they operate. Luckily, worksites do have regulations put in place by OSHA (Occupational Safety and Health Act), which enforces such regulations. They suggest that construction companies have training for their workers, that instructs them in slip, trip, and fall safety, as well has having a three step plan that prevents falls in the first place: plan, provide, and train.
What Are Basic Regulations for Equipment?
If you look up regulations for equipment, such as lifting equipment or lifting gear, the guidelines are pretty straightforward. The equipment must be ready to use, the right piece for the job assigned, and thoroughly marked. Examinations are also supposed to be scheduled regularly, with detailed records being kept. If defects are found, they should be reported right away and the machine taken off the workplace until it is in good condition again. Additionally, people operating equipment, such as lifting equipment, must have competent training and good supervision.
What is A Company’s Responsibility?
Construction companies are required to provide fall protection courses, which instruct workers in using fall protection equipment, such as guardrail systems, safety net systems, and personal fall arrest systems. Workers ought to know how to wear the systems and operate it the right way.
It is also a necessity for employers to give their workers the appropriate safety equipment and the right tools for the job they’re being asked to complete, such as ladders and scaffolds. Workers should have hazard recognition training and some may need to complete industrial rescue courses.
How Does It Benefit A Company to Have Excellent Safety Measures?
In the first place companies without such safety measures can get in serious trouble with the law, if a number of lawsuits regarding safety come up against it. They risk losing their business if they don’t comply with worksite regulations.
Apart from that, a positive trend has been occurring from 2008 to 2013. The number of accidents on worksites has been going down, thanks to better safety training and better equipment. Between 2008 and 2013, the accidents went down by 200 people. If your company is known for having outstanding safety training and measures put in place, more people will want to come work with you and other companies will want to have you as their contractor.
Fewer accidents are always a good thing and maintaining your equipment is a huge way to keep them from happening. Faulty and substandard equipment is to blame for a high percentage of workplace related accidents.Construction companies that take a real interest in training their employees well and maintaining high quality equipment have been shown to have less accidents and a longer time between them than companies who do not.
Make your company look good by implementing excellent safety training and keeping your machines and equipment up to date and inspected. It can make a huge difference for everyone.